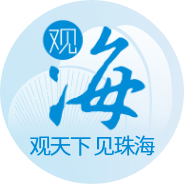
12月11日,在澳门回归祖国25周年纪念日前夕,作为港珠澳大桥西延线中的又一条大型跨海通道——黄茅海跨海通道正式通车,江门到珠海的时间缩短了约30分钟。
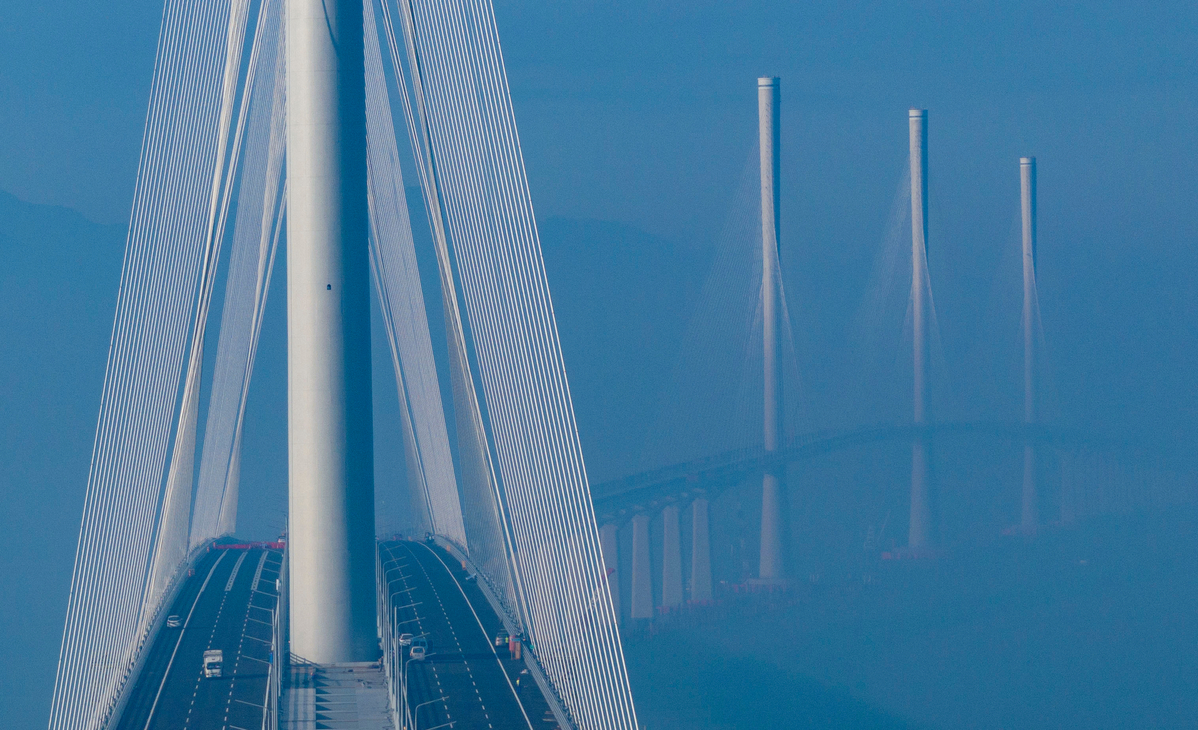
自2009年以来,15年间粤港澳大湾区已先后建成了港珠澳大桥、南沙大桥、深中通道、黄茅海跨海通道这4座大型跨海通道,形成了以南沙大桥和虎门大桥为“内环”、深中通道为“中环”、港珠澳大桥和黄茅海跨海通道共同构成“外环”的交通格局。尤其是“外环”的形成,便利的交通将加速港澳和粤西之间的要素流通。
“我有幸参与了大湾区这4座大型跨海工程的建设,它们的上部结构中均用上了钢箱梁,其制造技术,实现了从工厂化、自动化到数字化、智能化、智慧化的迭代升级,为大湾区的超级工程挺起了高质量‘脊梁’。”在当日举行的黄茅海跨海通道通车仪式上,中铁宝桥集团有限公司(以下简称“中铁宝桥”)舟山公司副总经理沙军强称。
“四化”建设理念,提升港珠澳大桥设计寿命到120年
被英国卫报称为“世界新七大奇迹之一”的港珠澳大桥,在今年6月24日举行的全国科技大会上,“港珠澳大桥跨海集群工程建造关键技术”获2023年度国家科技进步奖一等奖。
“港珠澳大桥的奇迹和荣誉,也有我们中铁宝桥的贡献,当年我们承担了其九洲航道桥4.3万吨的钢梁和钢塔的制造任务。”2012年10月,中铁宝桥中标港珠澳大桥CB05-G2标钢结构制造项目,时任中铁宝桥扬州公司钢箱梁生产车间负责人的沙军强,见证了每一节钢箱梁板单元的制造过程。
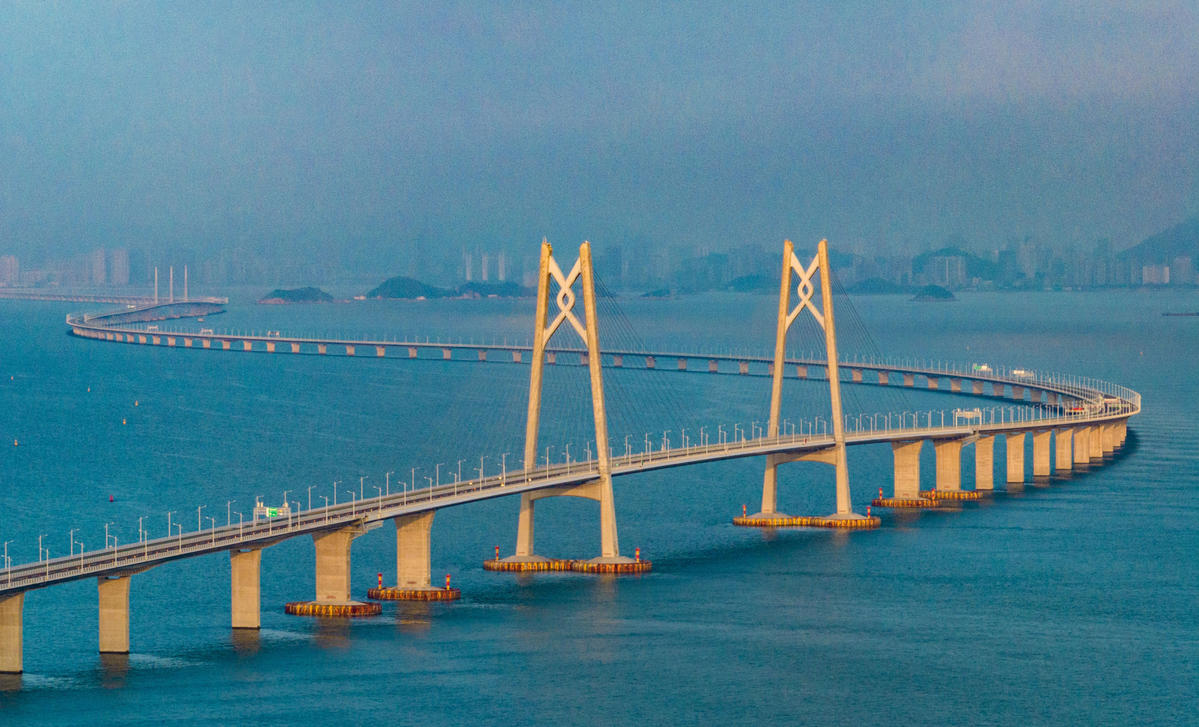
为确保大桥达到120年设计使用年限,港珠澳大桥管理局创新提出了“大型化、工厂化、标准化、装配化”的建设理念。“所有产品异地工厂制造,现场安装,把生产汽车的工序都用在造桥上了,这在全国的大桥建设中是首次。”谈及当年的生产要求,沙军强记忆犹新。
“大力实施创新驱动发展战略,这是党的十八大以后习近平总书记在广东发出的最强音。”时任中铁宝桥总经理助理、首席专家成宇海说,2012年集团投入巨资先后对江苏扬州、广东中山总拼基地进行了升级换代,对整个生产线进行了技术改造。
“此前建造大桥钢箱梁,都是在项目附近找块地搭建临时工棚,受风雨、高温的影响,工期无法保证,而且对下料、焊接、打磨、喷涂的质量都有影响,那个时候我们都是靠天吃饭,遇到天气不好的年份,项目部都要亏本。”沙军强称。
“工厂化、标准化为自动化生产和钢箱梁质量提供了保证。”沙军强告诉记者,工厂引进多项自动化生产设备和技术,并首次将数字化焊接机器人应用于钢箱梁制造,开创了国内钢箱梁自动化焊接的先河,全桥自动化焊接率达到90%,为实现大桥设计使用寿命120年提供了保障。
2015年2月10日,随着“天一号”3000吨运架一体船将港珠澳大桥CB05标最后一片组合梁稳稳放在桥墩上,港珠澳大桥CB05标率先拉通全标段。其中,组合梁的钢梁板单元在中铁宝桥集团扬州公司自动化生产线制造后,再将板单元通过江海联运至中山基地拼装,最后经喷砂、涂装后与存放桥面板组合安装。
经港珠澳大桥管理局委托驻厂监理及第三方检测公司对中铁宝桥生产制造的钢桥梁和钢塔焊缝检测,结果表明,无损伤制造、无损伤吊装、无损伤支撑的钢箱梁100%达到了大桥技术标准。
数字化应用,创造国内钢箱梁吊装的“南沙速度”
连接东莞与南沙的南沙大桥,于2019年4月2日建成通车,是《粤港澳大湾区发展规划纲要》发布后首个投入使用的大型跨海工程,也是缓解虎门大桥交通压力的民生工程。
中铁宝桥在圆满完成港珠澳大桥的钢箱梁制造任务后,2015年5月又中标了南沙大桥的大沙水道桥钢箱梁制造项目,该项目用钢量达2.92万吨。
南沙大桥全程采用的是标准八车道高速公路标准,其中大沙水道桥的主跨为1200米的双塔单跨钢箱梁悬索桥,刷新了我国悬索桥跨径的新纪录;钢箱梁的宽度49.7米,比港珠澳大桥钢箱梁的宽度33.1米还要宽16.6米。
面对新的挑战,中铁宝桥能否再次实现技术创新,成为扬州公司团队必须作答的课题。
“大湾区建设的每一个交通项目都对参建单位提出了科技创新的内在要求,我们也在努力通过创新将要求变成现实。”成宇海说。
在中铁宝桥的支持下,扬州公司大胆引进建筑行业中的建筑模型信息系统(BIM),在国内同行业中率先探索特大桥梁工程通过数字化创建立体模型提升钢箱梁生产速度。
“之前我们的产品设计用的都是平面图,引进BIM系统后,能通过电脑呈现出立体的钢箱梁模型,能看到钢箱梁的每一个空间,能看到钢箱梁的每一个数据。同时在电脑上可看到不同构件之间有没有碰撞,能及时发现设计时存在的问题,这样避免了问题产品成型后的改造和优化。”时任中铁宝桥南沙大桥项目公司副经理的沙军强说。
质量、安全和效率,一直是中铁宝桥的追求。在南沙大桥钢箱梁项目,中铁宝桥总结港珠澳大桥的经验,扩大车间长度,把钢箱梁制造与预拼装流水线都放在了扬州公司,并引进焊接设备远程群控技术,从而实现了全桥节段箱梁的装配化生产和预拼装。
“在这些创新举措的赋能下,我们提前一个月完成全桥94段钢箱梁制造预拼装任务,而且实现60天顺利完成吊装,比原计划提前7天完成,创造了国内钢箱梁吊装的‘南沙速度’。”回忆当年的战果,沙军强笑了。
智能化生产,建成“世界最大跨径海中悬索桥”
连接深圳和中山的深中通道,是继港珠澳大桥之后又一超大“隧、岛、桥”集群工程。在西人工岛驻足西望,深中通道的深中大桥已成为伶仃洋上一道亮丽的“天际线”。
“划”出这条线并不容易。深中大桥包含两座高270米的主塔,为保证通航能力,通航净高达76.5米,为世界最大跨径海中悬索桥。悬索桥由213个梁段组成,其钢箱梁由中铁宝桥等国内造桥单位联合建造并完成高空桥位连接。
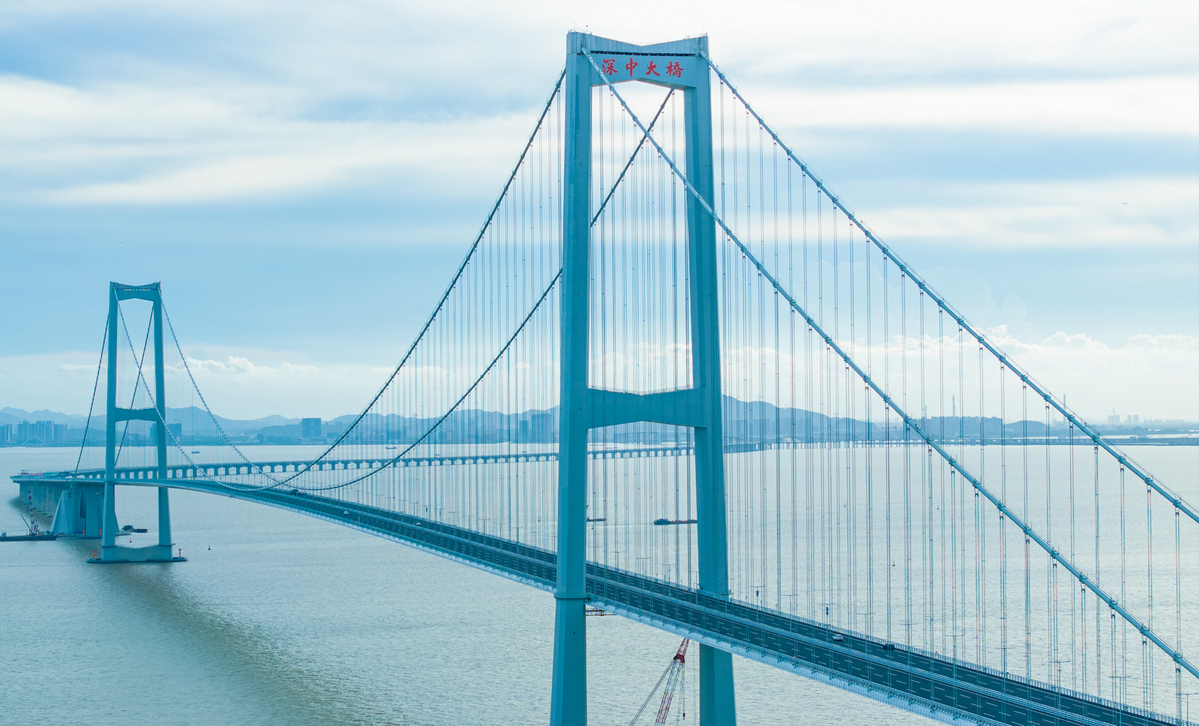
“在这个项目中,中铁宝桥承担的钢箱梁制造任务约9.1万吨。”时任深中通道项目公司常务副总经理的沙军强说,按照业主的要求,钢箱梁制造必须实现智能化,对钢箱梁的加工制造质量和工期控制提出了很高需求,作为施工企业,面临的压力和挑战都不小。
“我们把深中通道的钢箱梁放在扬州工厂制造。”沙军强坦言,在建设港珠澳大桥和南沙大桥项目时,该工厂的生产车间和设备已经实现了两次升级改造,多个环节实现了自动化。如果再次升级为智能化,既要再投入资金,又要面临着设备的淘汰,同时也面临着分流员工的压力。
“但我们更看到了智能化带来的产品质量、生产效率和市场竞争力,必须高标准打造智慧化工厂,为7年建成品质工程提供保障。”成宇海说。
为此,扬州公司首次提出以“四线一系统”为核心的钢箱梁智能制造理念,打造了一个拥有“板材智能下料生产线、板单元智能焊接生产线、节段智能总拼生产线、钢箱梁智能涂装生产线及智能制造执行管控系统”的智慧工厂。
在板单元智能焊接生产线中,公司联合有关厂家首次研发内焊机器人,对折弯成U型的钢板实现了双面埋弧全熔透焊接,成功破解了无法双面焊接全熔透的行业共性难题。“最令我们自豪的是,产品一次检验合格率达99%以上,较传统接头提升钢桥面板疲劳耐久性100%以上,并提高生产效率30%以上。”沙军强说。
深中通道在《粤港澳大湾区发展规划纲要》发布五周年之际正式通车,通车首日,通车量达10万辆次,一跃成为大湾区的“新顶流”。
“AI+焊接”,特殊结构件实现全自动生产
黄茅海跨海通道港是珠澳大桥西延线中的重要节段之一。从港珠澳大桥珠海公路口岸出发,一路向西,途经港珠澳大桥连接线、洪鹤大桥、鹤港高速,至黄茅海跨海通道以西终点,全程约84公里。
黄茅海跨海通道是《粤港澳大湾区发展规划纲要》发布后,首个在大湾区开工的大型跨海通道项目,2020年,中铁宝桥中标了黄茅海跨海通道控制性工程之一的黄茅海大桥6万吨钢箱梁制造任务。
“在中标之前,我们研判了大湾区的发展态势,根据扬州工厂升级智能化生产线后人员分流的需求,中铁宝桥集团依托浙江舟山岛的航道优势,在舟山岛购置513亩土地成立了舟山公司,为大湾区项目打造了一个年产钢箱梁能力达15万-20万吨的智慧化工厂。”时任舟山公司副总经理、中铁宝桥黄茅海跨海通道项目负责人的沙军强说。
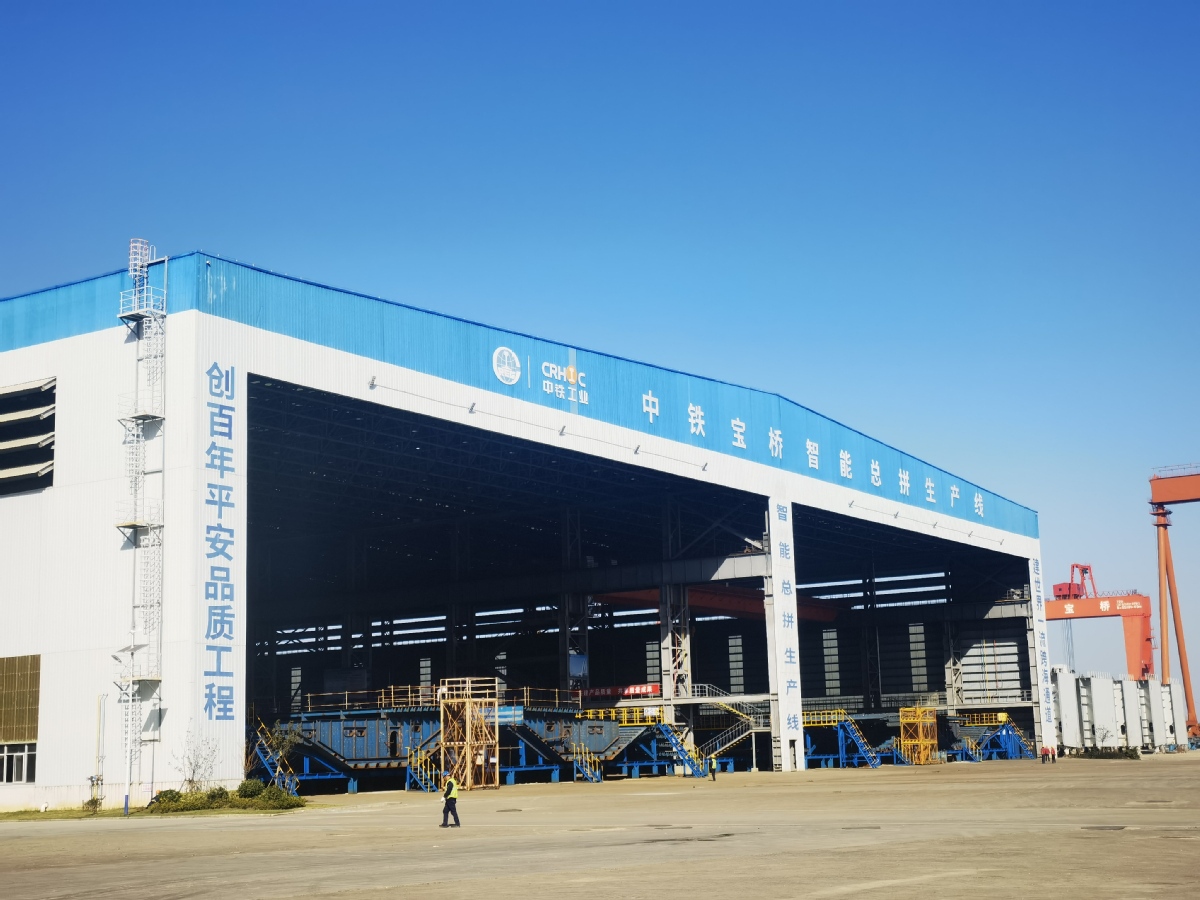
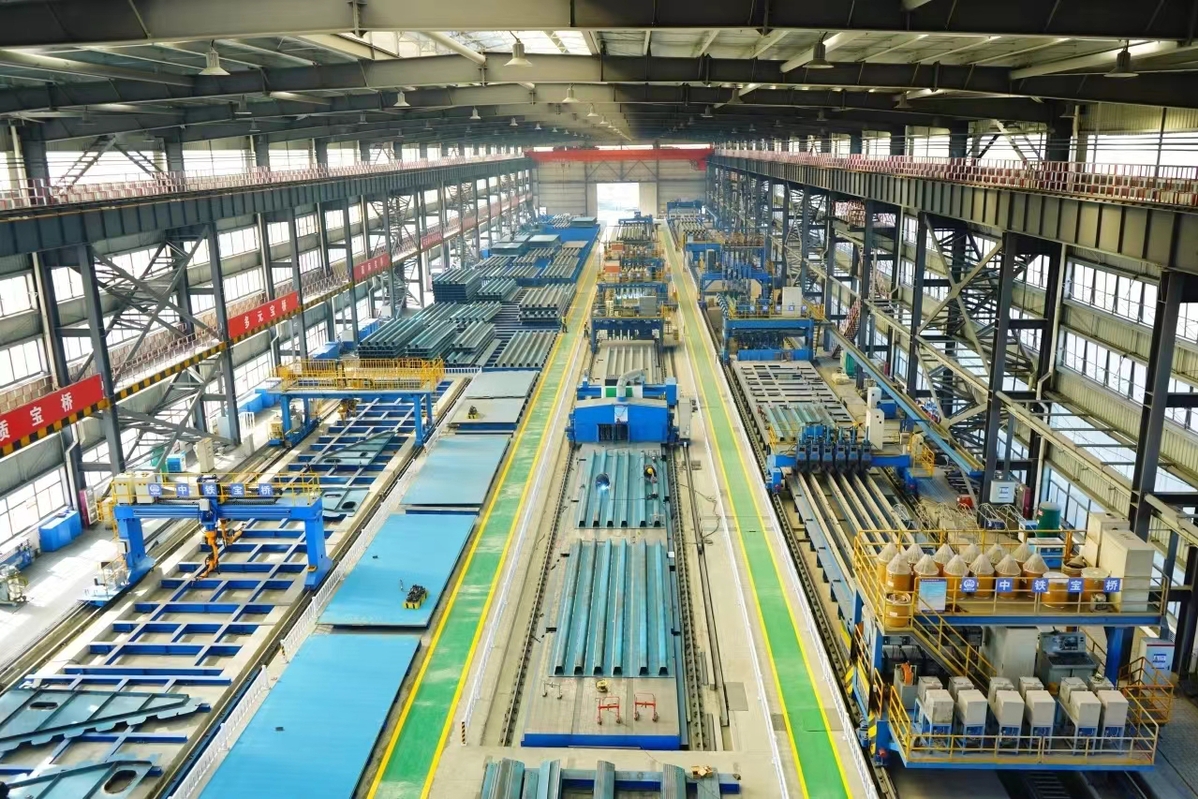
“这个智慧化工厂就是为黄茅海大桥项目量身定做的。”据舟山公司总工程师吴江波介绍,大桥防撞钢护栏是每座桥梁的必需配置,之前他们没有生产防撞钢护栏,接到订单后也是从其他企业订制。但是,订制的产品没有办法实现智能化和集成化生产,质量达不到最佳要求。为此,公司特意为黄茅海钢箱梁量身定做了一个智慧化工厂。
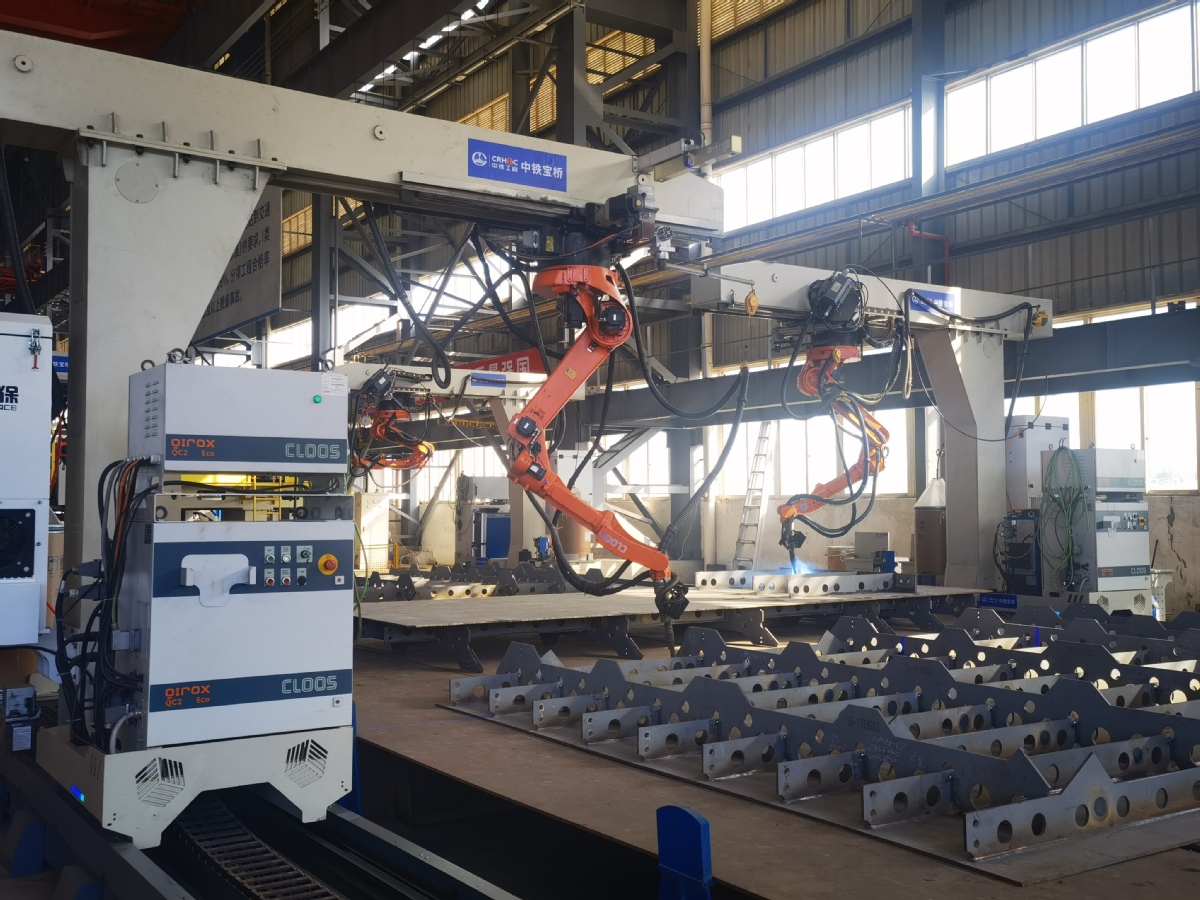
为此,舟山公司在建立“四线一系统”的基础上,又建立了国内首条多边形防撞钢护栏智能制造生产线,实现了桥梁钢结构的智能化和集成化生产,解决了料件规格尺寸不规则、焊缝外观不一致性的难题。“防撞钢护栏产品一次报检合格率提高至99%以上,为黄茅海大桥的高品质建设提供了一流的技术和设备保证,也提升了产品的市场竞争力。”沙军强补充道。
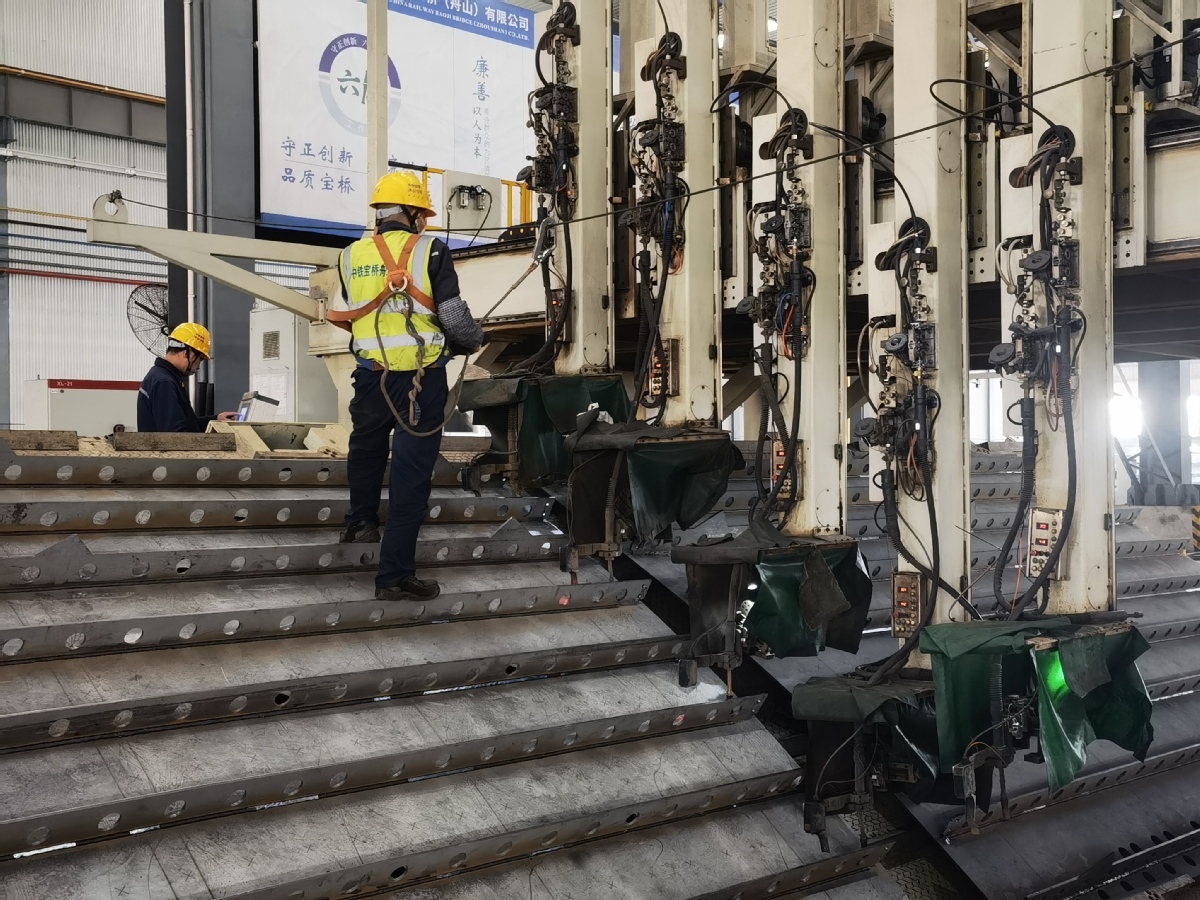
“针对钢箱梁的特殊结构件,首次研发应用‘AI+焊接’融合技术。”在舟山公司技术部,负责焊接工艺的副部长郭瑞告诉记者,其中“AI+焊接”融合技术,即通过摄像头、激光传感器等设备以及逆向建模技术,实现了对桥梁结构件的自动扫描、自动辨别形状及焊缝、自动调取焊接工艺库数据、自动焊接的智能化和自动化生产,彻底改变传统离线和在线编程的繁琐工序,有效提高了产品质量的一致性。
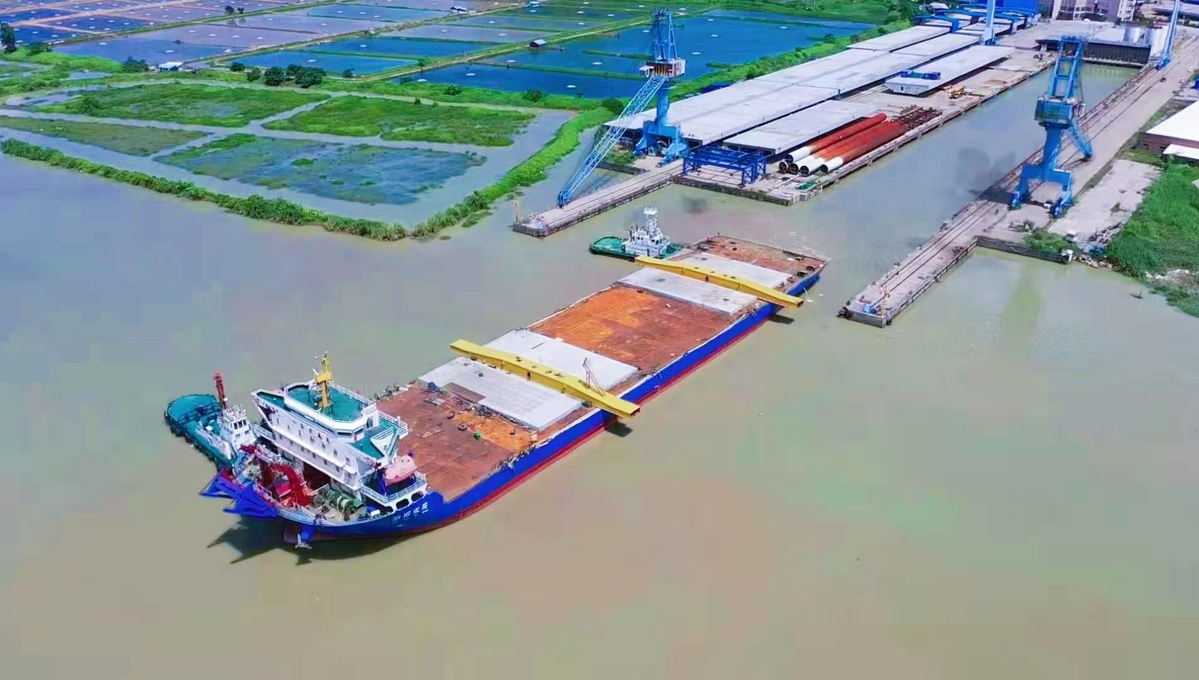
创新永不止步,创新才有未来。历经4年多的建设,如今黄茅海跨海通道正式通车,从江门到港珠澳大桥,驱车大约只需50分钟,港珠澳大桥经贸新通道的作用日益凸显;沙军强也开启了他在大湾区的第五座超级工程——狮子洋通道的建设,他们的钢箱梁技术创新故事还在继续。
12月11日,在澳门回归祖国25周年纪念日前夕,作为港珠澳大桥西延线中的又一条大型跨海通道——黄茅海跨海通道正式通车,江门到珠海的时间缩短了约30分钟。
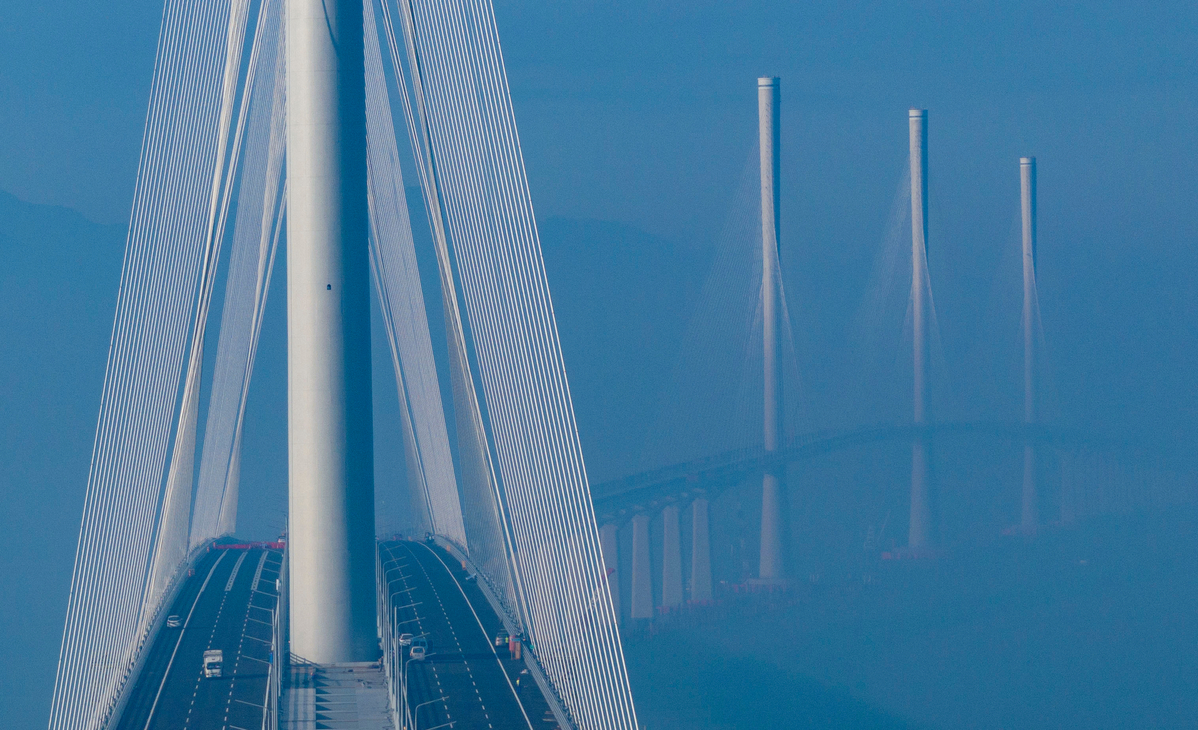
自2009年以来,15年间粤港澳大湾区已先后建成了港珠澳大桥、南沙大桥、深中通道、黄茅海跨海通道这4座大型跨海通道,形成了以南沙大桥和虎门大桥为“内环”、深中通道为“中环”、港珠澳大桥和黄茅海跨海通道共同构成“外环”的交通格局。尤其是“外环”的形成,便利的交通将加速港澳和粤西之间的要素流通。
“我有幸参与了大湾区这4座大型跨海工程的建设,它们的上部结构中均用上了钢箱梁,其制造技术,实现了从工厂化、自动化到数字化、智能化、智慧化的迭代升级,为大湾区的超级工程挺起了高质量‘脊梁’。”在当日举行的黄茅海跨海通道通车仪式上,中铁宝桥集团有限公司(以下简称“中铁宝桥”)舟山公司副总经理沙军强称。
“四化”建设理念,提升港珠澳大桥设计寿命到120年
被英国卫报称为“世界新七大奇迹之一”的港珠澳大桥,在今年6月24日举行的全国科技大会上,“港珠澳大桥跨海集群工程建造关键技术”获2023年度国家科技进步奖一等奖。
“港珠澳大桥的奇迹和荣誉,也有我们中铁宝桥的贡献,当年我们承担了其九洲航道桥4.3万吨的钢梁和钢塔的制造任务。”2012年10月,中铁宝桥中标港珠澳大桥CB05-G2标钢结构制造项目,时任中铁宝桥扬州公司钢箱梁生产车间负责人的沙军强,见证了每一节钢箱梁板单元的制造过程。
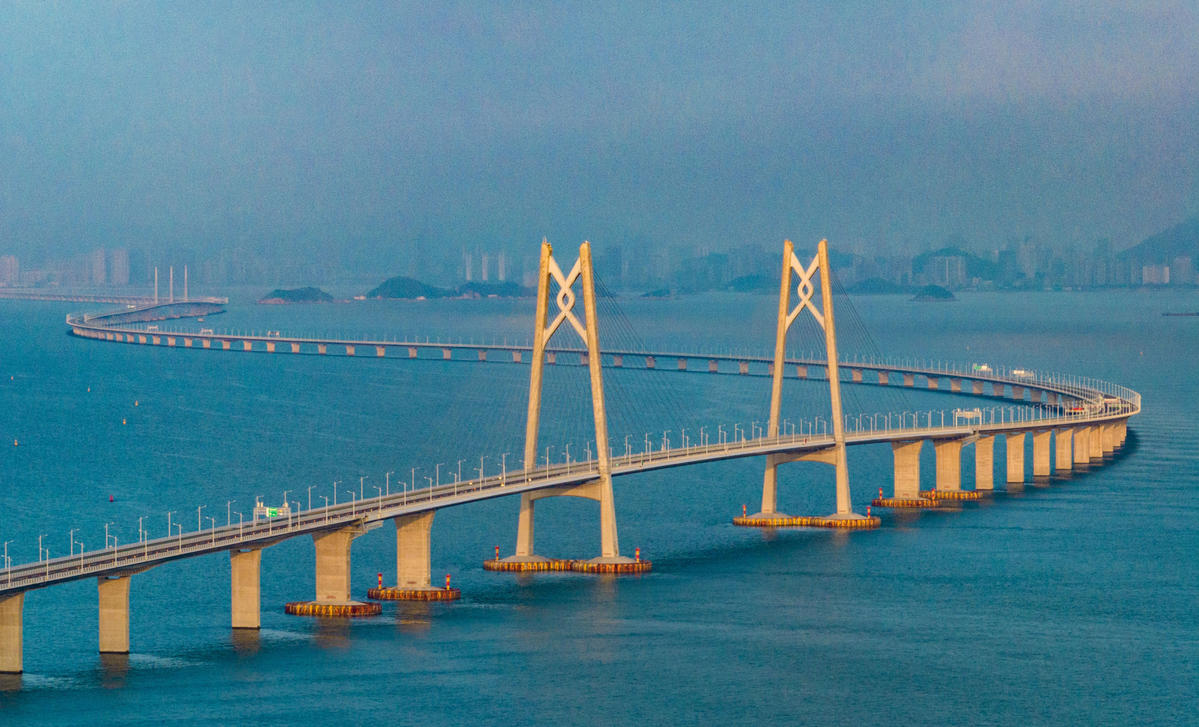
为确保大桥达到120年设计使用年限,港珠澳大桥管理局创新提出了“大型化、工厂化、标准化、装配化”的建设理念。“所有产品异地工厂制造,现场安装,把生产汽车的工序都用在造桥上了,这在全国的大桥建设中是首次。”谈及当年的生产要求,沙军强记忆犹新。
“大力实施创新驱动发展战略,这是党的十八大以后习近平总书记在广东发出的最强音。”时任中铁宝桥总经理助理、首席专家成宇海说,2012年集团投入巨资先后对江苏扬州、广东中山总拼基地进行了升级换代,对整个生产线进行了技术改造。
“此前建造大桥钢箱梁,都是在项目附近找块地搭建临时工棚,受风雨、高温的影响,工期无法保证,而且对下料、焊接、打磨、喷涂的质量都有影响,那个时候我们都是靠天吃饭,遇到天气不好的年份,项目部都要亏本。”沙军强称。
“工厂化、标准化为自动化生产和钢箱梁质量提供了保证。”沙军强告诉记者,工厂引进多项自动化生产设备和技术,并首次将数字化焊接机器人应用于钢箱梁制造,开创了国内钢箱梁自动化焊接的先河,全桥自动化焊接率达到90%,为实现大桥设计使用寿命120年提供了保障。
2015年2月10日,随着“天一号”3000吨运架一体船将港珠澳大桥CB05标最后一片组合梁稳稳放在桥墩上,港珠澳大桥CB05标率先拉通全标段。其中,组合梁的钢梁板单元在中铁宝桥集团扬州公司自动化生产线制造后,再将板单元通过江海联运至中山基地拼装,最后经喷砂、涂装后与存放桥面板组合安装。
经港珠澳大桥管理局委托驻厂监理及第三方检测公司对中铁宝桥生产制造的钢桥梁和钢塔焊缝检测,结果表明,无损伤制造、无损伤吊装、无损伤支撑的钢箱梁100%达到了大桥技术标准。
数字化应用,创造国内钢箱梁吊装的“南沙速度”
连接东莞与南沙的南沙大桥,于2019年4月2日建成通车,是《粤港澳大湾区发展规划纲要》发布后首个投入使用的大型跨海工程,也是缓解虎门大桥交通压力的民生工程。
中铁宝桥在圆满完成港珠澳大桥的钢箱梁制造任务后,2015年5月又中标了南沙大桥的大沙水道桥钢箱梁制造项目,该项目用钢量达2.92万吨。
南沙大桥全程采用的是标准八车道高速公路标准,其中大沙水道桥的主跨为1200米的双塔单跨钢箱梁悬索桥,刷新了我国悬索桥跨径的新纪录;钢箱梁的宽度49.7米,比港珠澳大桥钢箱梁的宽度33.1米还要宽16.6米。
面对新的挑战,中铁宝桥能否再次实现技术创新,成为扬州公司团队必须作答的课题。
“大湾区建设的每一个交通项目都对参建单位提出了科技创新的内在要求,我们也在努力通过创新将要求变成现实。”成宇海说。
在中铁宝桥的支持下,扬州公司大胆引进建筑行业中的建筑模型信息系统(BIM),在国内同行业中率先探索特大桥梁工程通过数字化创建立体模型提升钢箱梁生产速度。
“之前我们的产品设计用的都是平面图,引进BIM系统后,能通过电脑呈现出立体的钢箱梁模型,能看到钢箱梁的每一个空间,能看到钢箱梁的每一个数据。同时在电脑上可看到不同构件之间有没有碰撞,能及时发现设计时存在的问题,这样避免了问题产品成型后的改造和优化。”时任中铁宝桥南沙大桥项目公司副经理的沙军强说。
质量、安全和效率,一直是中铁宝桥的追求。在南沙大桥钢箱梁项目,中铁宝桥总结港珠澳大桥的经验,扩大车间长度,把钢箱梁制造与预拼装流水线都放在了扬州公司,并引进焊接设备远程群控技术,从而实现了全桥节段箱梁的装配化生产和预拼装。
“在这些创新举措的赋能下,我们提前一个月完成全桥94段钢箱梁制造预拼装任务,而且实现60天顺利完成吊装,比原计划提前7天完成,创造了国内钢箱梁吊装的‘南沙速度’。”回忆当年的战果,沙军强笑了。
智能化生产,建成“世界最大跨径海中悬索桥”
连接深圳和中山的深中通道,是继港珠澳大桥之后又一超大“隧、岛、桥”集群工程。在西人工岛驻足西望,深中通道的深中大桥已成为伶仃洋上一道亮丽的“天际线”。
“划”出这条线并不容易。深中大桥包含两座高270米的主塔,为保证通航能力,通航净高达76.5米,为世界最大跨径海中悬索桥。悬索桥由213个梁段组成,其钢箱梁由中铁宝桥等国内造桥单位联合建造并完成高空桥位连接。
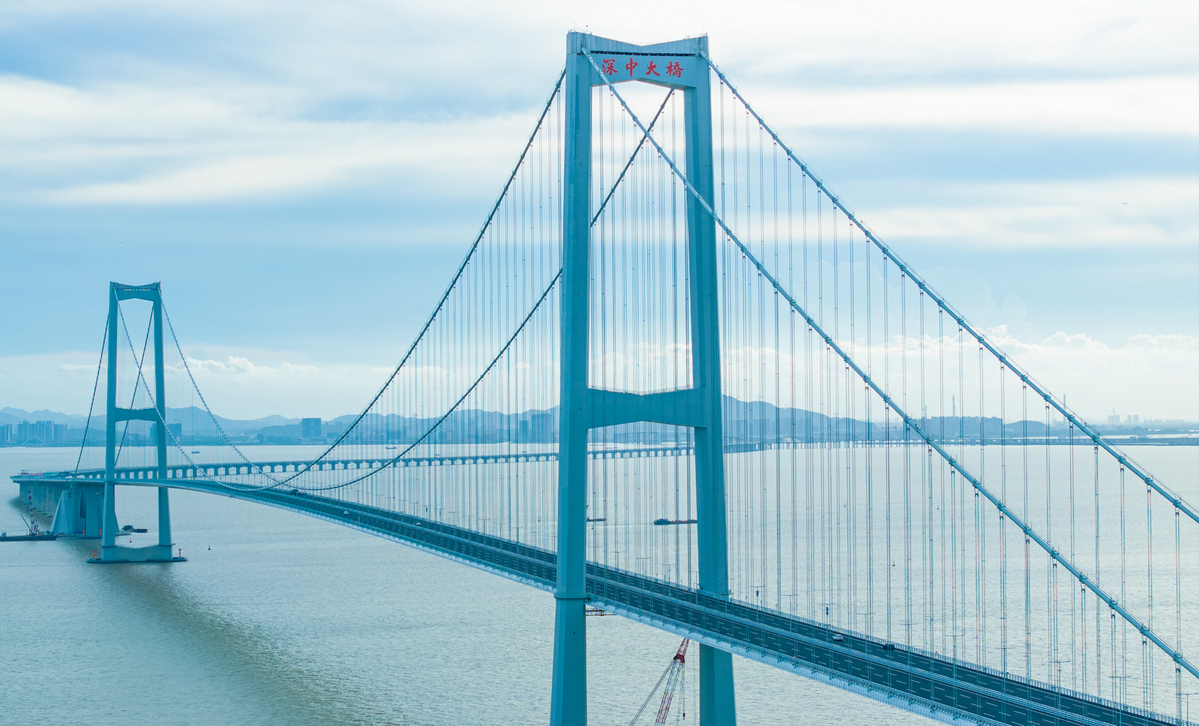
“在这个项目中,中铁宝桥承担的钢箱梁制造任务约9.1万吨。”时任深中通道项目公司常务副总经理的沙军强说,按照业主的要求,钢箱梁制造必须实现智能化,对钢箱梁的加工制造质量和工期控制提出了很高需求,作为施工企业,面临的压力和挑战都不小。
“我们把深中通道的钢箱梁放在扬州工厂制造。”沙军强坦言,在建设港珠澳大桥和南沙大桥项目时,该工厂的生产车间和设备已经实现了两次升级改造,多个环节实现了自动化。如果再次升级为智能化,既要再投入资金,又要面临着设备的淘汰,同时也面临着分流员工的压力。
“但我们更看到了智能化带来的产品质量、生产效率和市场竞争力,必须高标准打造智慧化工厂,为7年建成品质工程提供保障。”成宇海说。
为此,扬州公司首次提出以“四线一系统”为核心的钢箱梁智能制造理念,打造了一个拥有“板材智能下料生产线、板单元智能焊接生产线、节段智能总拼生产线、钢箱梁智能涂装生产线及智能制造执行管控系统”的智慧工厂。
在板单元智能焊接生产线中,公司联合有关厂家首次研发内焊机器人,对折弯成U型的钢板实现了双面埋弧全熔透焊接,成功破解了无法双面焊接全熔透的行业共性难题。“最令我们自豪的是,产品一次检验合格率达99%以上,较传统接头提升钢桥面板疲劳耐久性100%以上,并提高生产效率30%以上。”沙军强说。
深中通道在《粤港澳大湾区发展规划纲要》发布五周年之际正式通车,通车首日,通车量达10万辆次,一跃成为大湾区的“新顶流”。
“AI+焊接”,特殊结构件实现全自动生产
黄茅海跨海通道港是珠澳大桥西延线中的重要节段之一。从港珠澳大桥珠海公路口岸出发,一路向西,途经港珠澳大桥连接线、洪鹤大桥、鹤港高速,至黄茅海跨海通道以西终点,全程约84公里。
黄茅海跨海通道是《粤港澳大湾区发展规划纲要》发布后,首个在大湾区开工的大型跨海通道项目,2020年,中铁宝桥中标了黄茅海跨海通道控制性工程之一的黄茅海大桥6万吨钢箱梁制造任务。
“在中标之前,我们研判了大湾区的发展态势,根据扬州工厂升级智能化生产线后人员分流的需求,中铁宝桥集团依托浙江舟山岛的航道优势,在舟山岛购置513亩土地成立了舟山公司,为大湾区项目打造了一个年产钢箱梁能力达15万-20万吨的智慧化工厂。”时任舟山公司副总经理、中铁宝桥黄茅海跨海通道项目负责人的沙军强说。
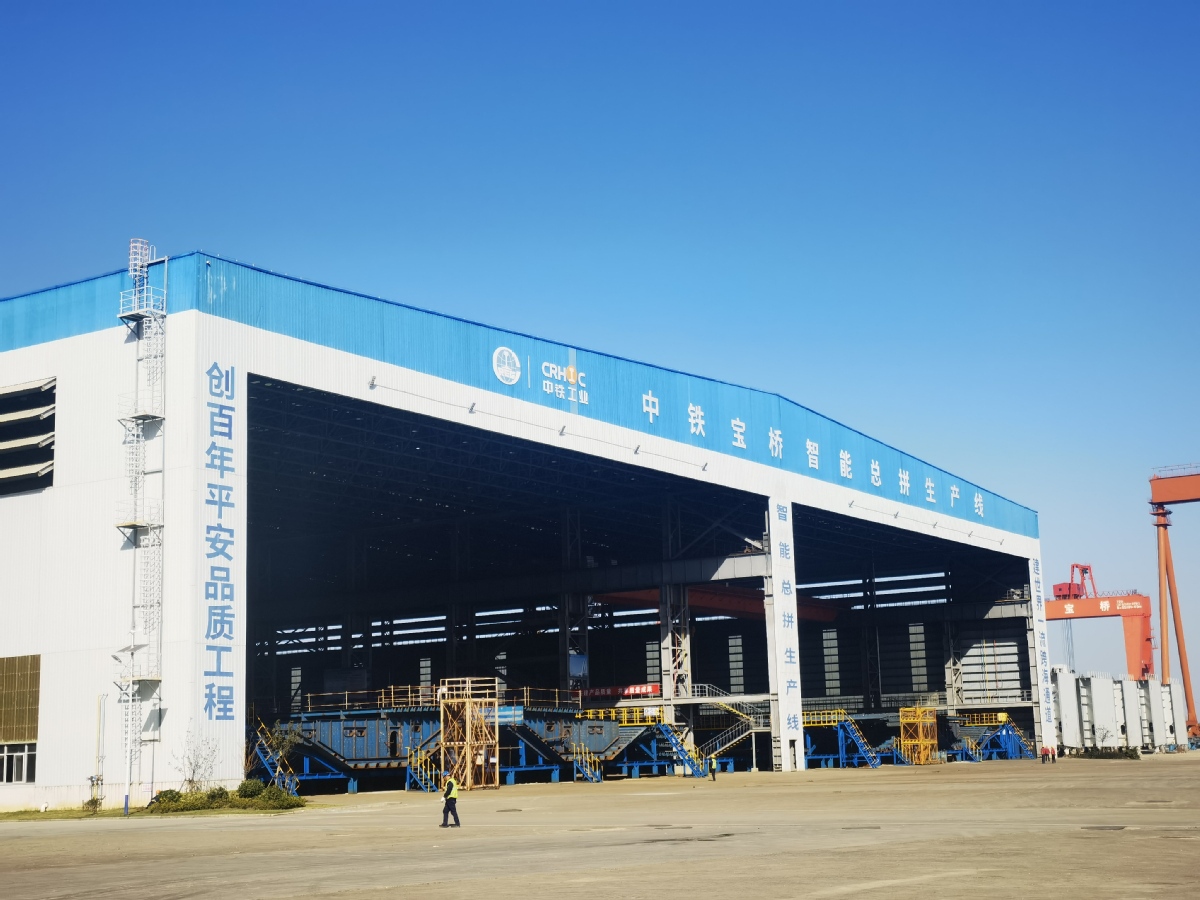
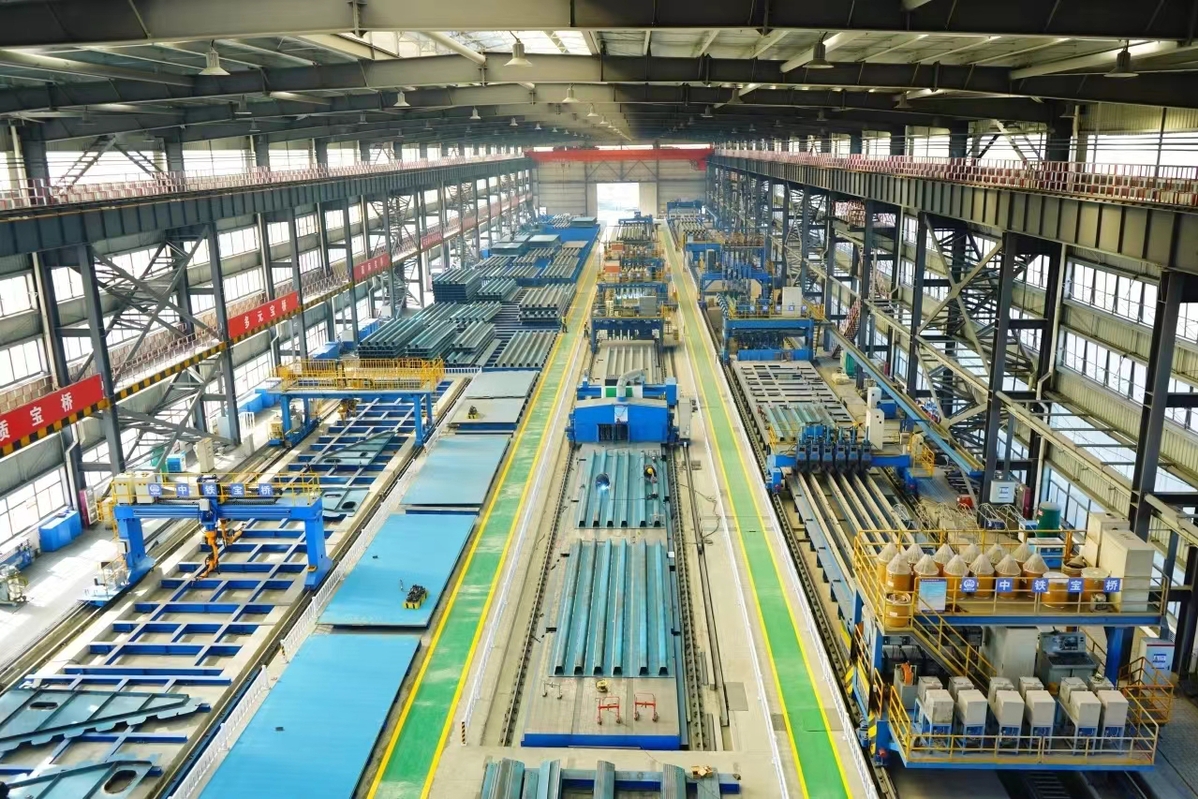
“这个智慧化工厂就是为黄茅海大桥项目量身定做的。”据舟山公司总工程师吴江波介绍,大桥防撞钢护栏是每座桥梁的必需配置,之前他们没有生产防撞钢护栏,接到订单后也是从其他企业订制。但是,订制的产品没有办法实现智能化和集成化生产,质量达不到最佳要求。为此,公司特意为黄茅海钢箱梁量身定做了一个智慧化工厂。
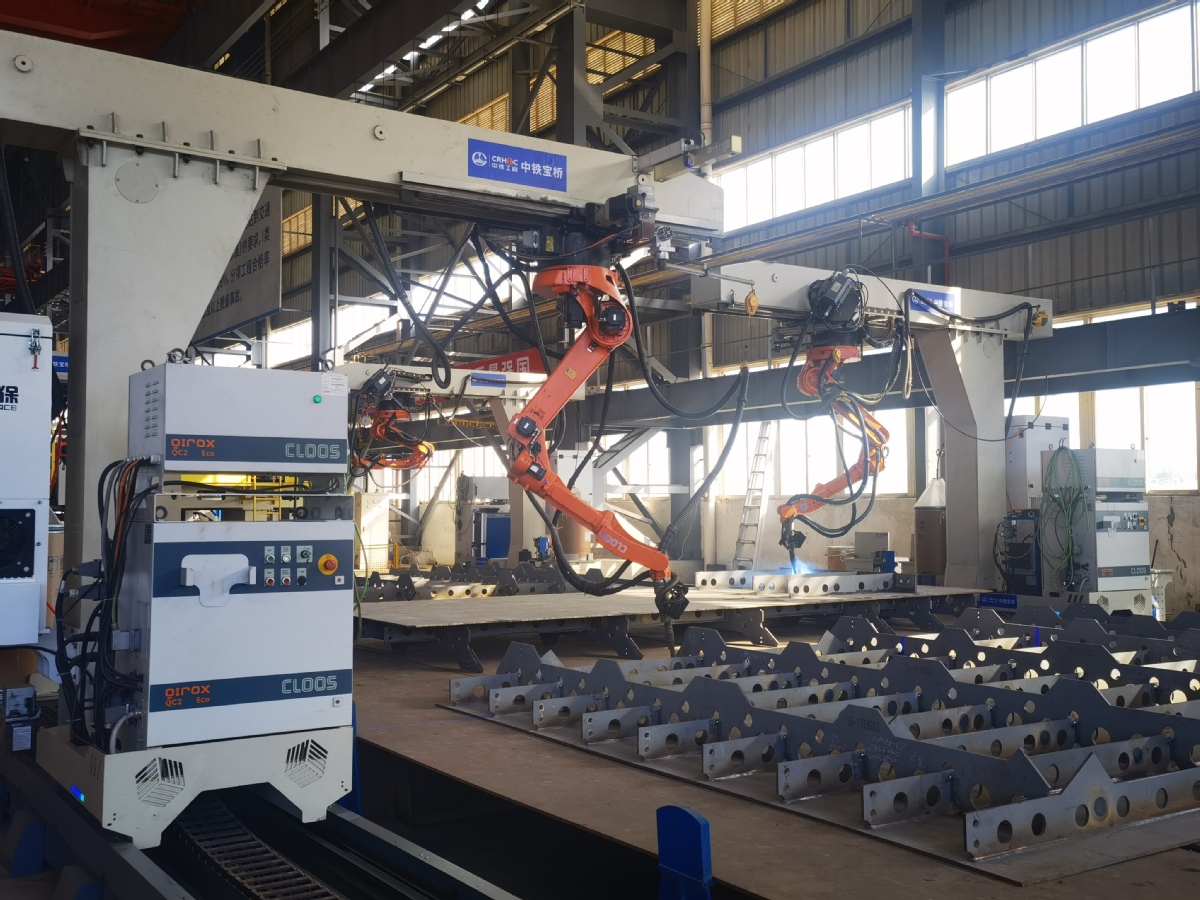
为此,舟山公司在建立“四线一系统”的基础上,又建立了国内首条多边形防撞钢护栏智能制造生产线,实现了桥梁钢结构的智能化和集成化生产,解决了料件规格尺寸不规则、焊缝外观不一致性的难题。“防撞钢护栏产品一次报检合格率提高至99%以上,为黄茅海大桥的高品质建设提供了一流的技术和设备保证,也提升了产品的市场竞争力。”沙军强补充道。
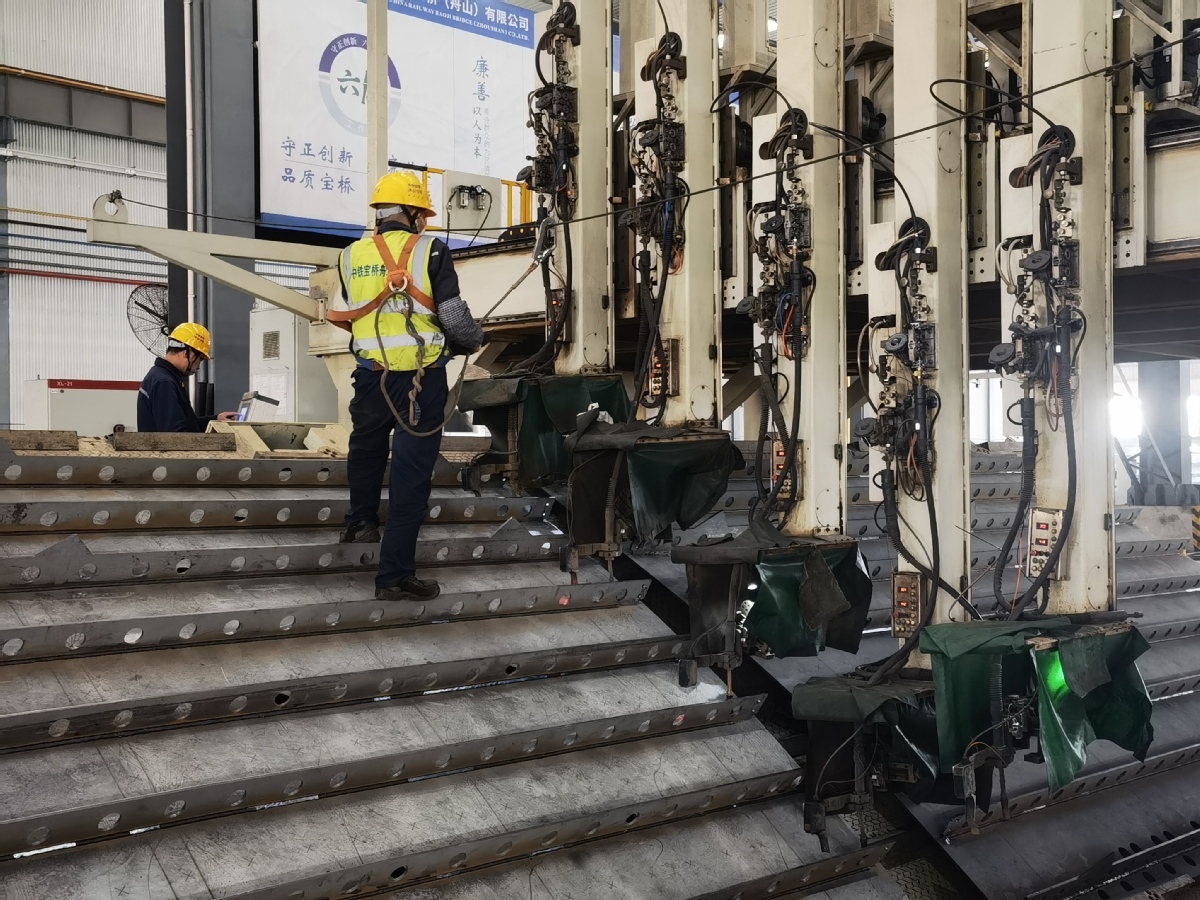
“针对钢箱梁的特殊结构件,首次研发应用‘AI+焊接’融合技术。”在舟山公司技术部,负责焊接工艺的副部长郭瑞告诉记者,其中“AI+焊接”融合技术,即通过摄像头、激光传感器等设备以及逆向建模技术,实现了对桥梁结构件的自动扫描、自动辨别形状及焊缝、自动调取焊接工艺库数据、自动焊接的智能化和自动化生产,彻底改变传统离线和在线编程的繁琐工序,有效提高了产品质量的一致性。
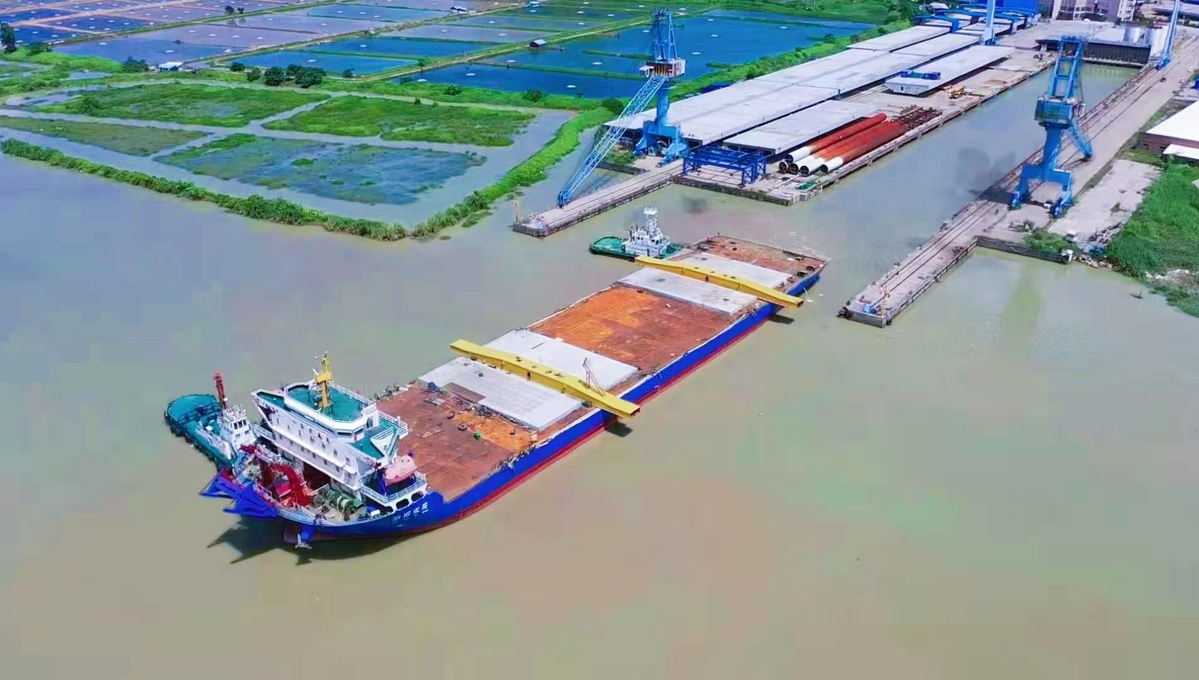
创新永不止步,创新才有未来。历经4年多的建设,如今黄茅海跨海通道正式通车,从江门到港珠澳大桥,驱车大约只需50分钟,港珠澳大桥经贸新通道的作用日益凸显;沙军强也开启了他在大湾区的第五座超级工程——狮子洋通道的建设,他们的钢箱梁技术创新故事还在继续。
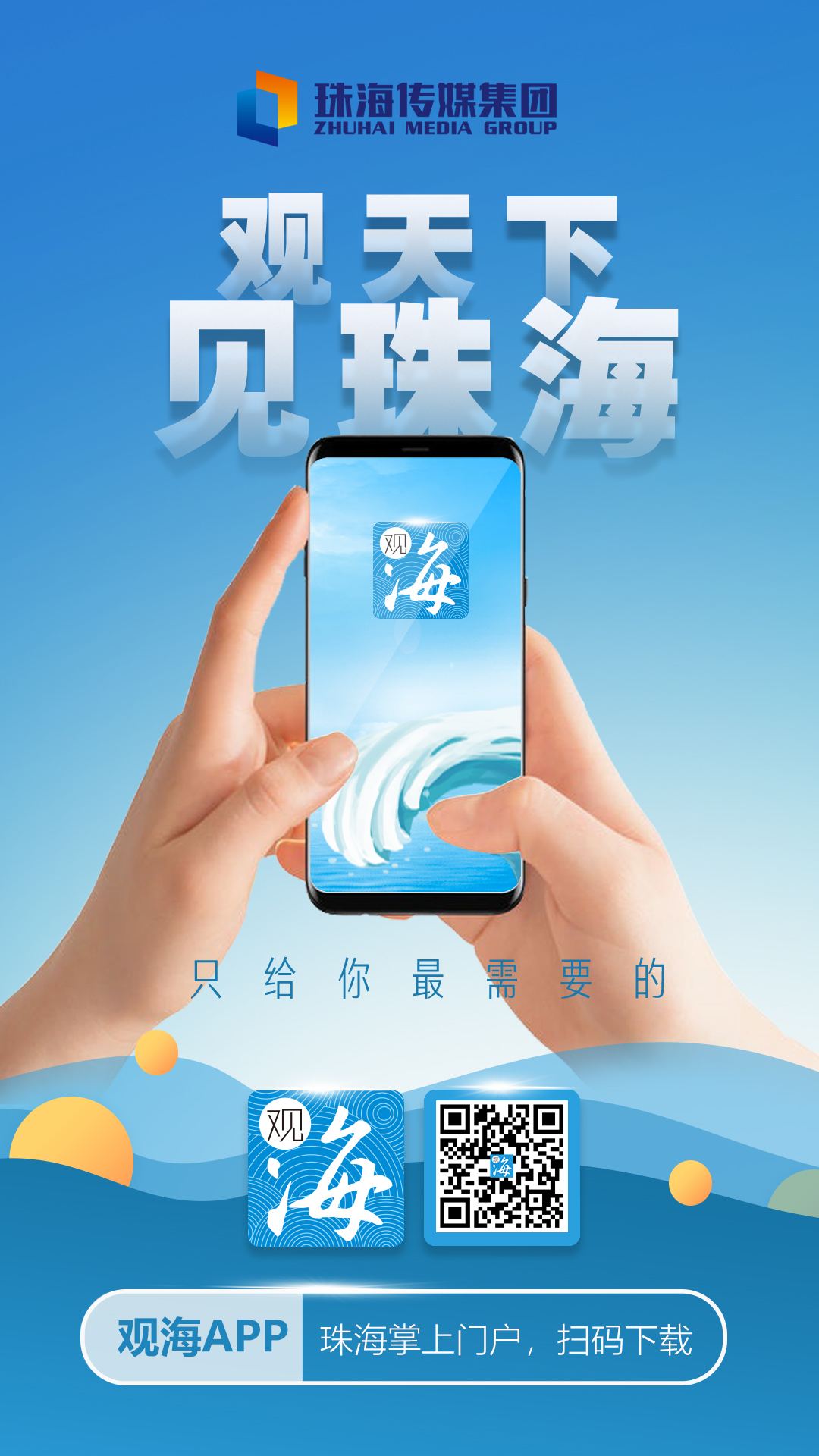
-我已经到底线啦-
暂时没有评论